MC6100 Series
CVD Coated Grade for Steel Turning
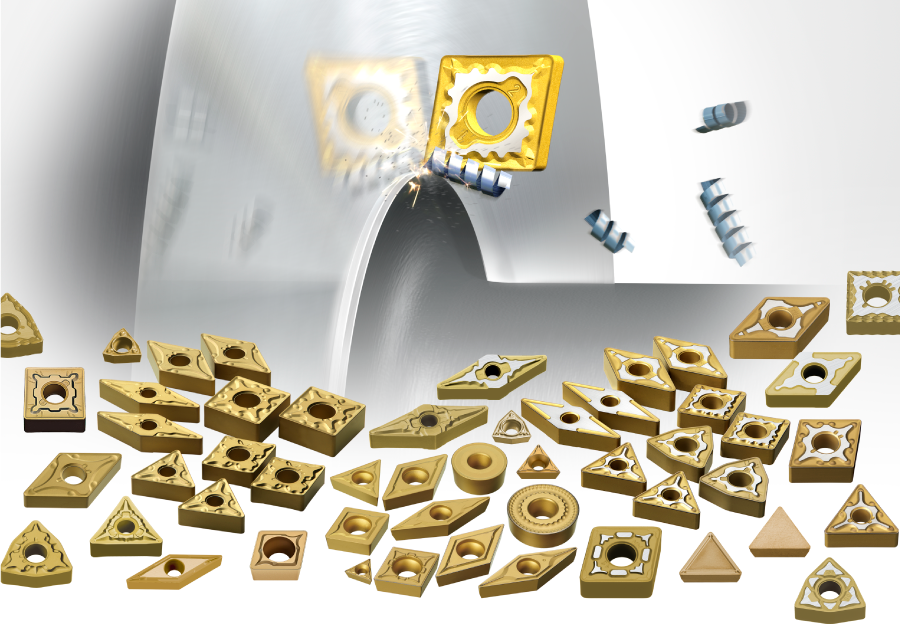
Bringing the Ultimate High Speed
Cutting Performance
CVD Coated Grade for Steel Turning MC6115 / MC6125 / MC6135
Dramatic increase in stability and wear resistance, enabled by utilising the improved coating adhesion and crystal orientation technology.
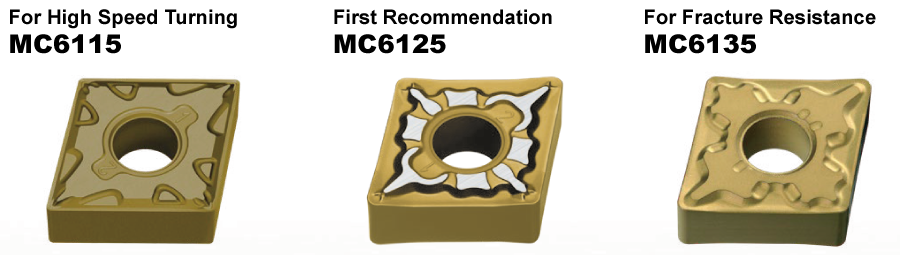
The addition of positive and negative inserts enables a wide range of machining such as boring and finishing.
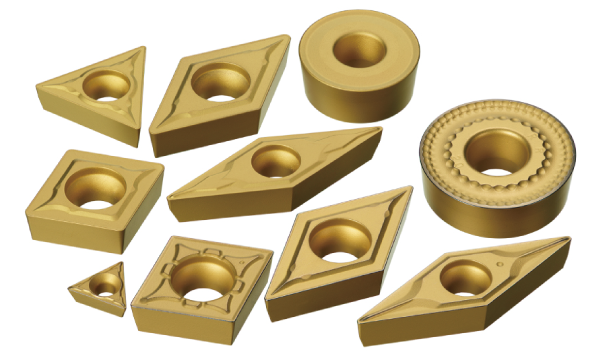
"Super" Nano Texture Technology
The standard Nano Texture Technology has been improved and developed to be an industry leading standard for crystal growth of Al2O3 coatings. This Super Nano Texture Technology increases tool life and wear resistance due to the fine, dense crystal growth process.
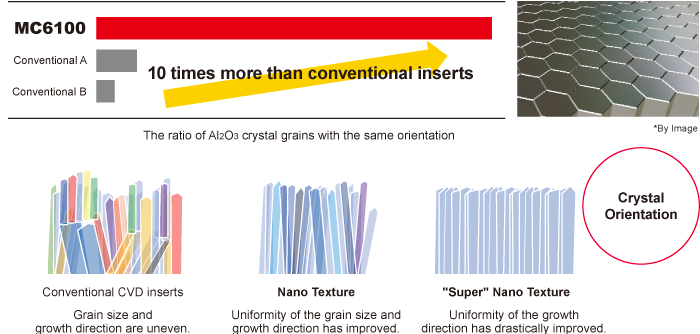
Super TOUGH-Grip
The Super TOUGH-Grip layer has finer crystal grains that enhance the strength of the adhesion between the coating layers.
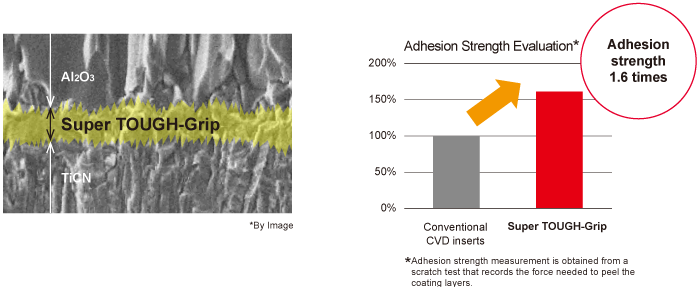
Protection Against Sudden Fracturing
Cracks that occur during unstable machining are prevented due to the relaxing of the tensile stress in the coating. MC6100 series has an 80% reduction in coating tensile stress compared to conventional CVD inserts.
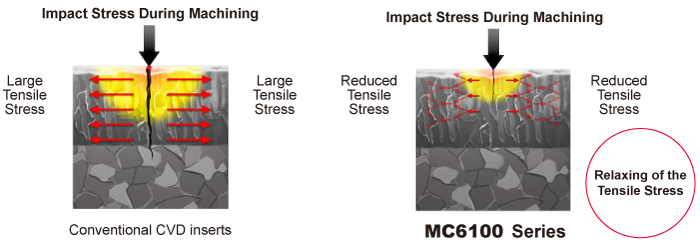
Cracks are generated in the surface of coatings during machining. They propagate through the coating into the substrate due to the large tensile stress in the coating structure. This creates one of the main causes of sudden insert breakage.
MC6100 Series has a much lower level of stress than conventional CVD coatings due to the surface treatment. This divides the force of impacts during machining and protects from sudden fracturing.
MC6135
Optimal versatility for machining continuous through to intermittent applications.
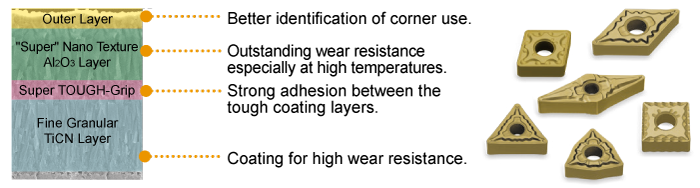
Thinner Coatings Optimised for General Purpose Machining
Industry-leading crystal orientation control technology enables thinner but still impact-resistant coatings provide improved chipping and wear resistance which is optimal for general-purpose use. (50% thinner compared to our conventional coating).
Machining SCM440 : Comparison of Toughness During Interrupted Cutting
MC6135 shows high stability even during interrupted cutting and can be used over a wide area of applications.
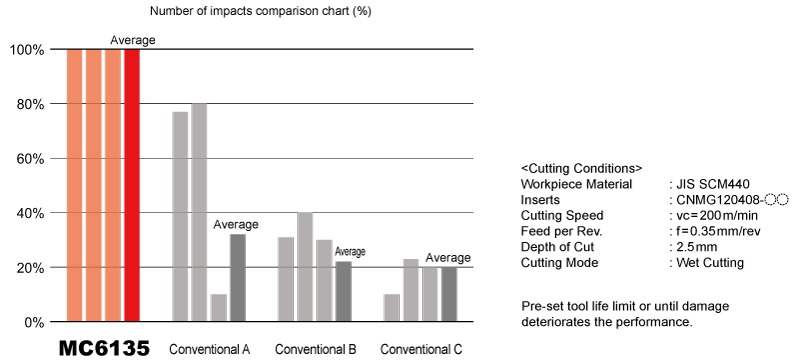
MC6125
First recommended grade for steel turning.
Increasing tool life with stable performance over a wider range of applications.
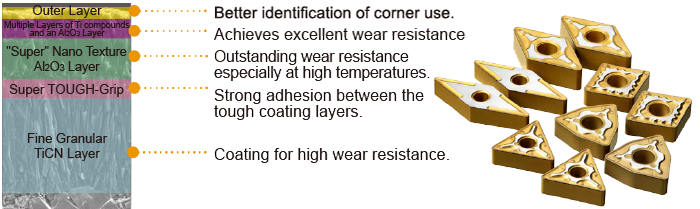
Special Smooth Surface Treatment
MC6125 uses a new surface treatment for the cutting edge for increased stability. Additionally, the seating faces also have a special smooth surface treatment that provides improved clamping stability to enable a wider range of applications.
Machining S45C : Comparison of Wear Resistance
The surface treatment has improved stability and provided longer tool life.
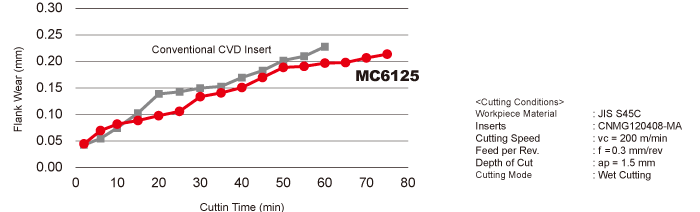
MC6115
MC6115 improves high speed machining and process efficiency with a dramatic increase in resistance to wear and heat.
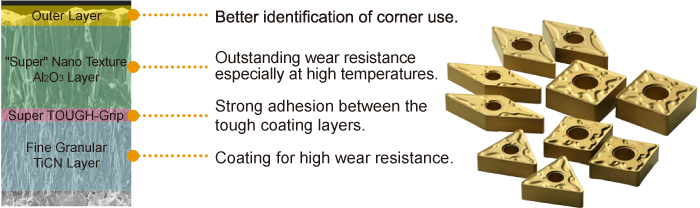
Improved Outer Coating (Layer)
The outer layer of MC6115 restricts chip welding thereby improving the dimensional accuracy and surface roughness of components. This also enables easy recognition of whether the corner can continue machining.
Example when machining Scr420H
When comparing the high edge strength MH breaker with a conventional low resistance chip breaker, it shows that MC6115 accomplishes both high welding and wear resistance.
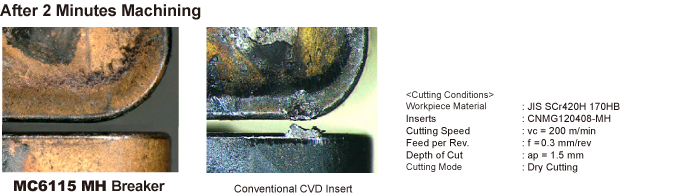
FPH Breaker
The combination of a positive land cutting edge shape and a two-stage protrusion optimises chip generation at low depths of cut, high feed conditions, thereby reducing machining times.
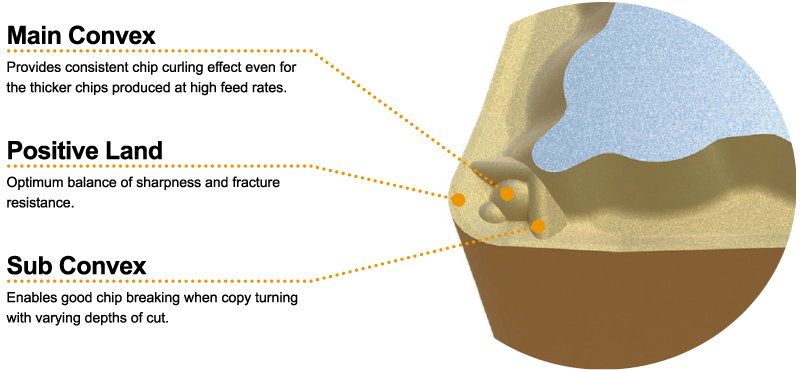
SCM440 : Comparison of Chips and Finished Surface
The FPH chipbreaker has excellent chip breaking properties, Therefore a good component surface finish can always be expected.
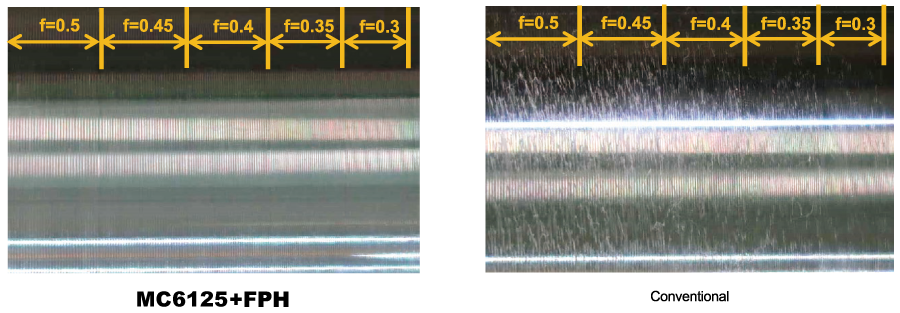
Material : JIS SCM440, Inserts : CNMG120408-oo MC6125, Cutting Speed : vc=200m/min
Depth of Cut : 0.2mm, Feed per Rev. : f= The fluctuation values are shown in the image.
Cutting Mode : Wet Cutting
Chip Comparison
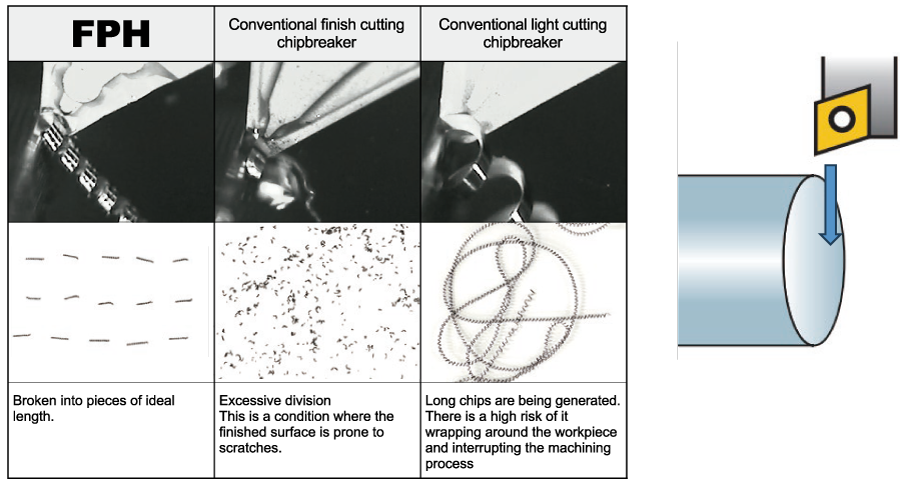
Material : JIS SCM440, Inserts : DNMG150408-oo, Cutting Speed : vc=200m/min
Depth of Cut : 0.2mm, Feed per Rev. : f=0.3mm/rev, Cutting Mode : Dry Cutting
Cutting Performance
Machining SCr420H : Comparison of Wear Resistance During Continuous Wet Cutting
The thick coating exclusively for MC6125 highly suppresses early wear.
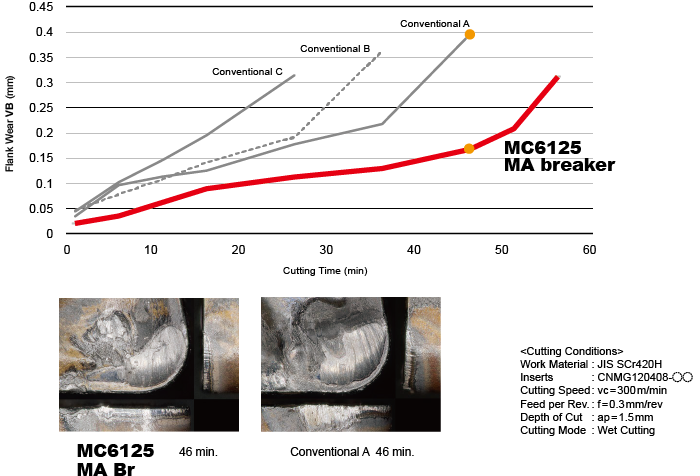
Comparison of Toughness During Interrupted Cutting
Provides stable cutting under severe cutting conditions that are likely to cause sudden fracturing.
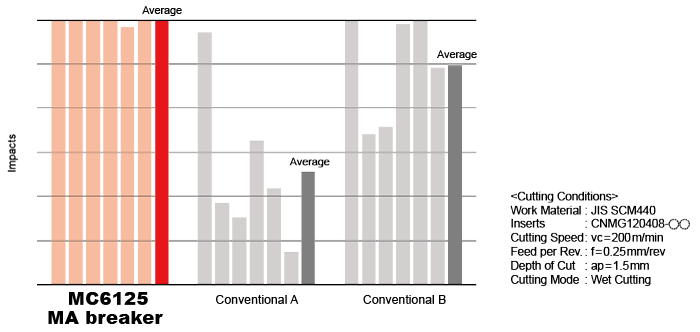
Machining S45C : Comparison of Wear Resistance During Continuous Dry Cutting
The "Super" Nano Texture Technology increases tool life even when dry cutting by suppressing crater wear.
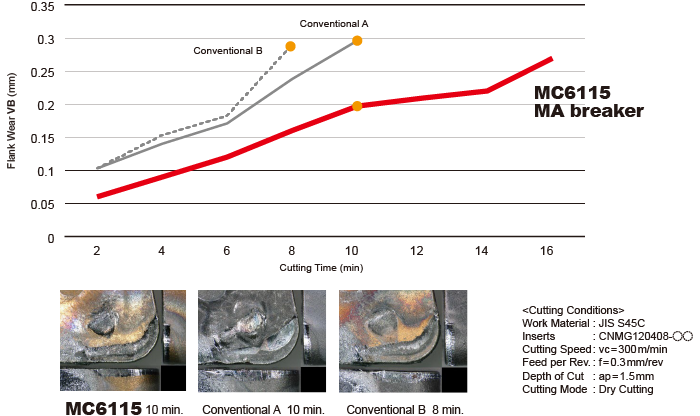
Machining SUJ2 : Comparison of Wear Resistance During Continuous Wet Cutting
The thick coating provides high flank wear resistance.

Examples of Usage
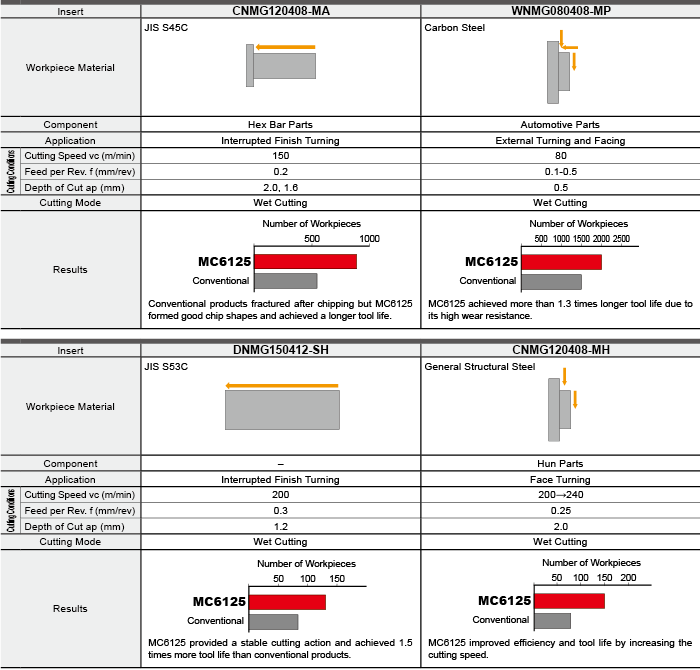
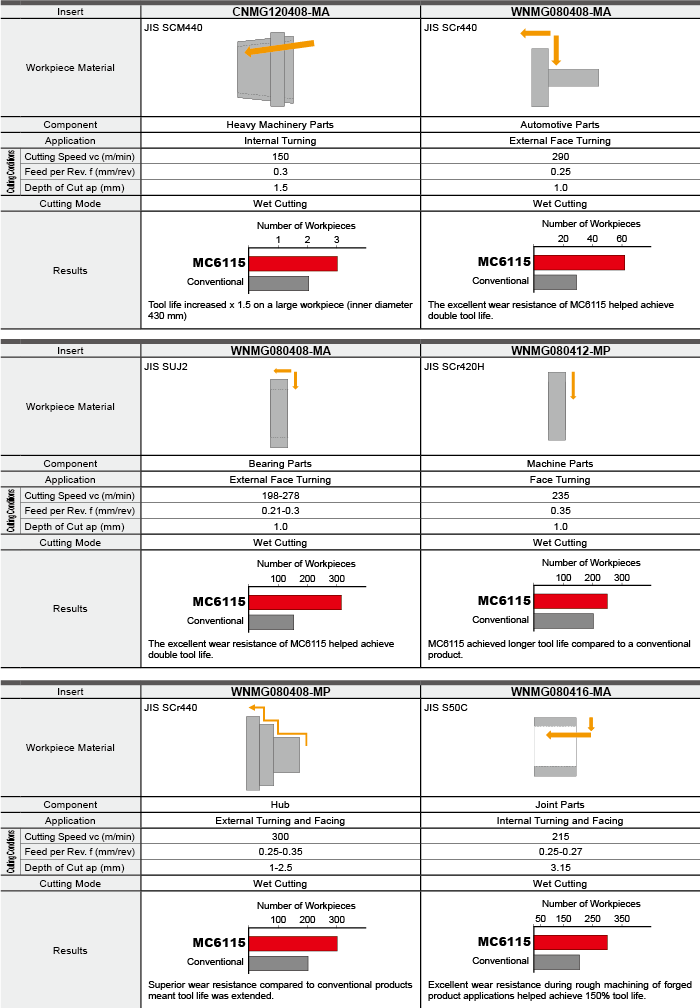
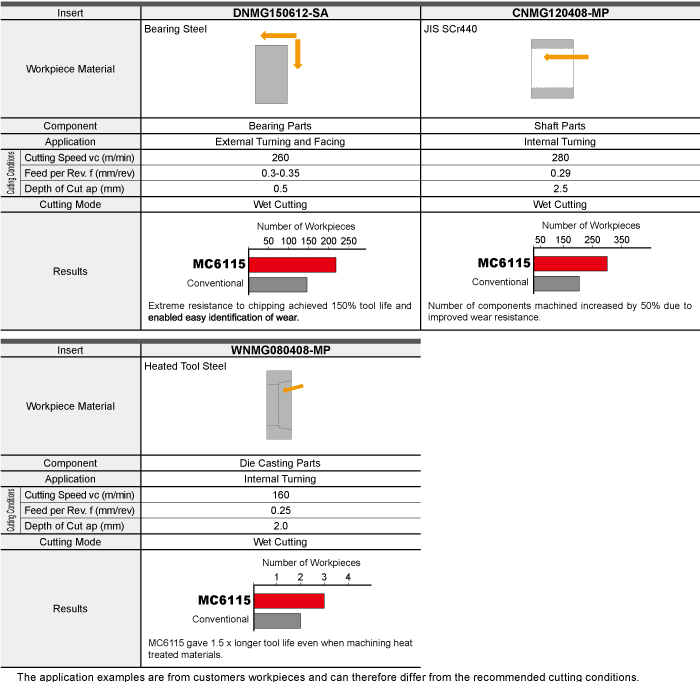
Technical consultation from here
24/7Contact form