MV
The future is here – New MV grades turning and milling inserts
Mitsubishi Materials has developed a special series of CVD coated grades that reaches across applications for both milling and turning
Benefits
MV milling Inserts
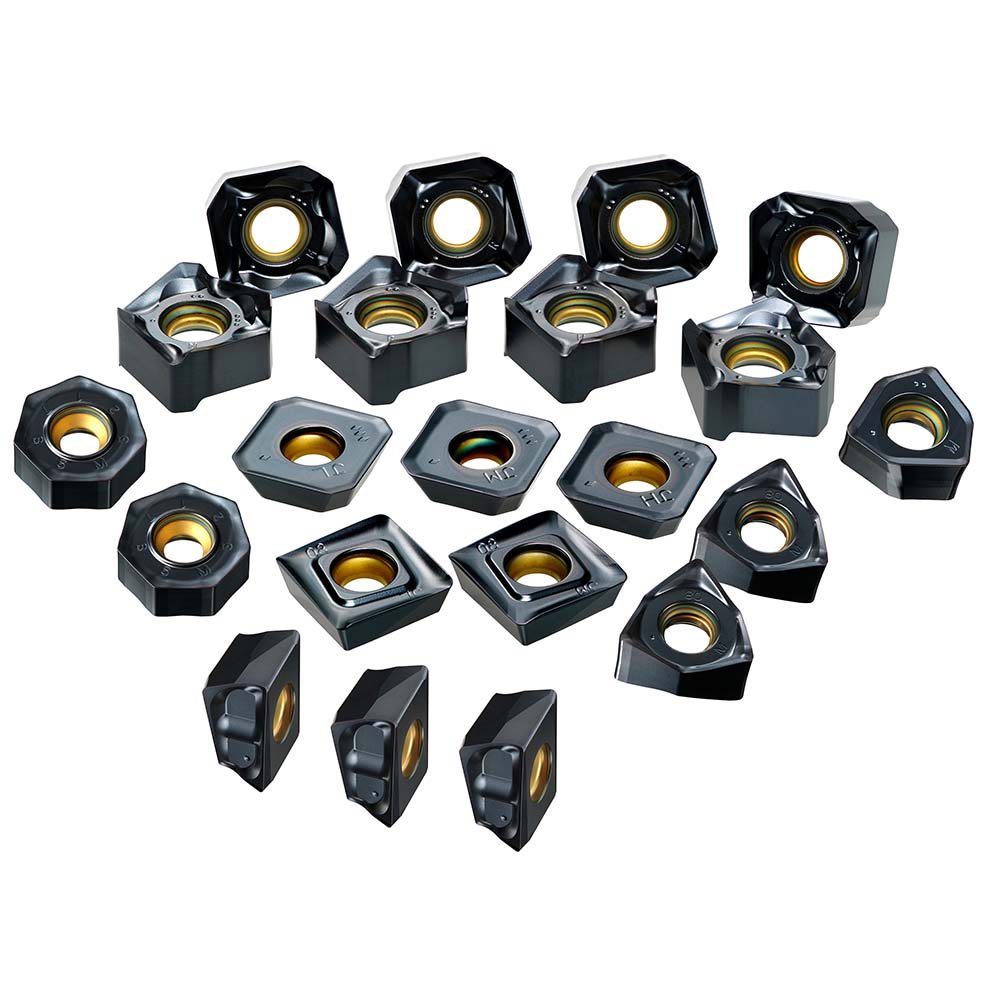
The ultimate all round grade available for milling and turning
- The new CVD coating technology provides dramatic improvements in hardness for longer tool life.
- Reduces tool change time by enabling better consistency of dimensional accuracy and surface finishes.
- Thermal cracking is prevented and coolant can be used. Coolant is especially important for tool life for efficient machining of stainless steels.
Technology
The combination of atoms with different sizes creates an exceptionally hard crystal structure.
Technology creates usability
The hardness of (Al,Ti)N increases as the Al content ratio increases, but with conventional technology, when the Al content ratio exceeds 60 %, the crystal structure changes and the hardness of (Al,Ti)N decreases.
Using a new CVD coating process based on Mitsubishi Materials‘ own original technology. This a way in which the Al-Rich coating does not change its crystal structure even when the Al content is increased. This enables a higher Al content and a provides a higher hardness (Al,Ti)N.
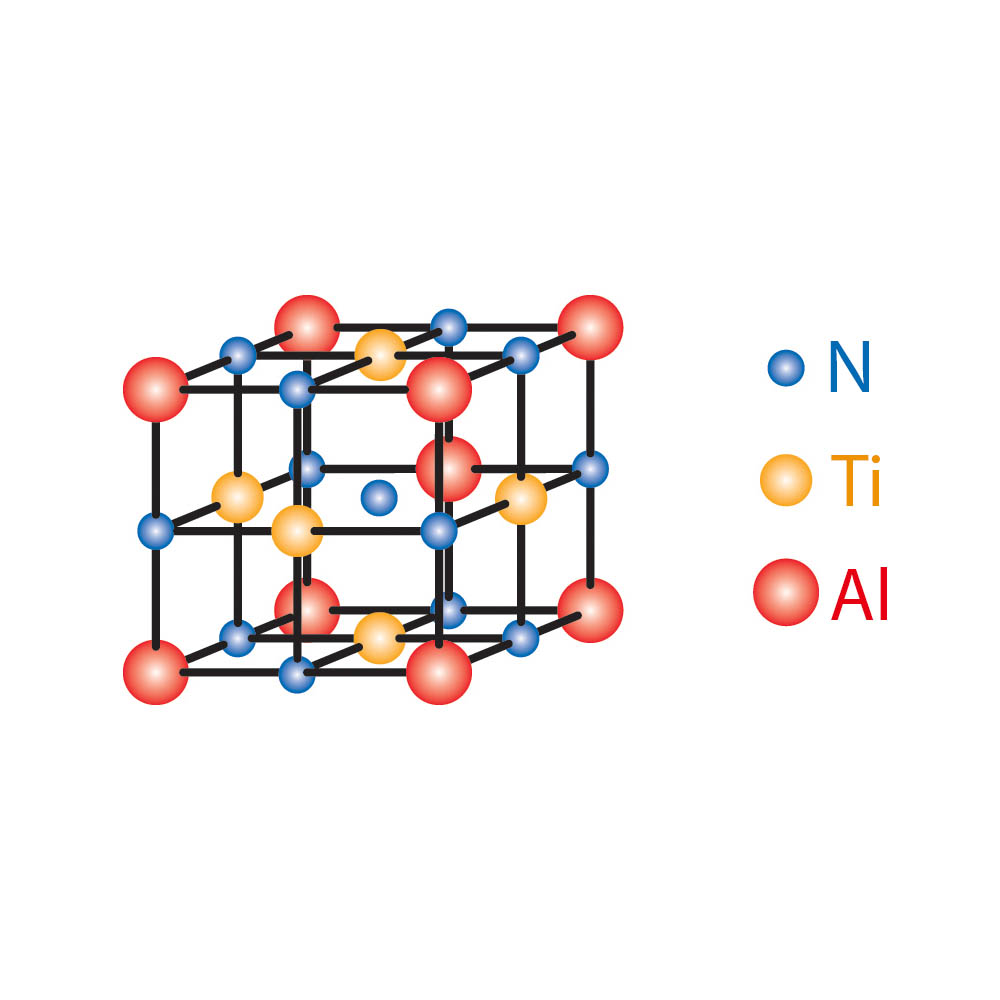
Availability
MV turning Inserts
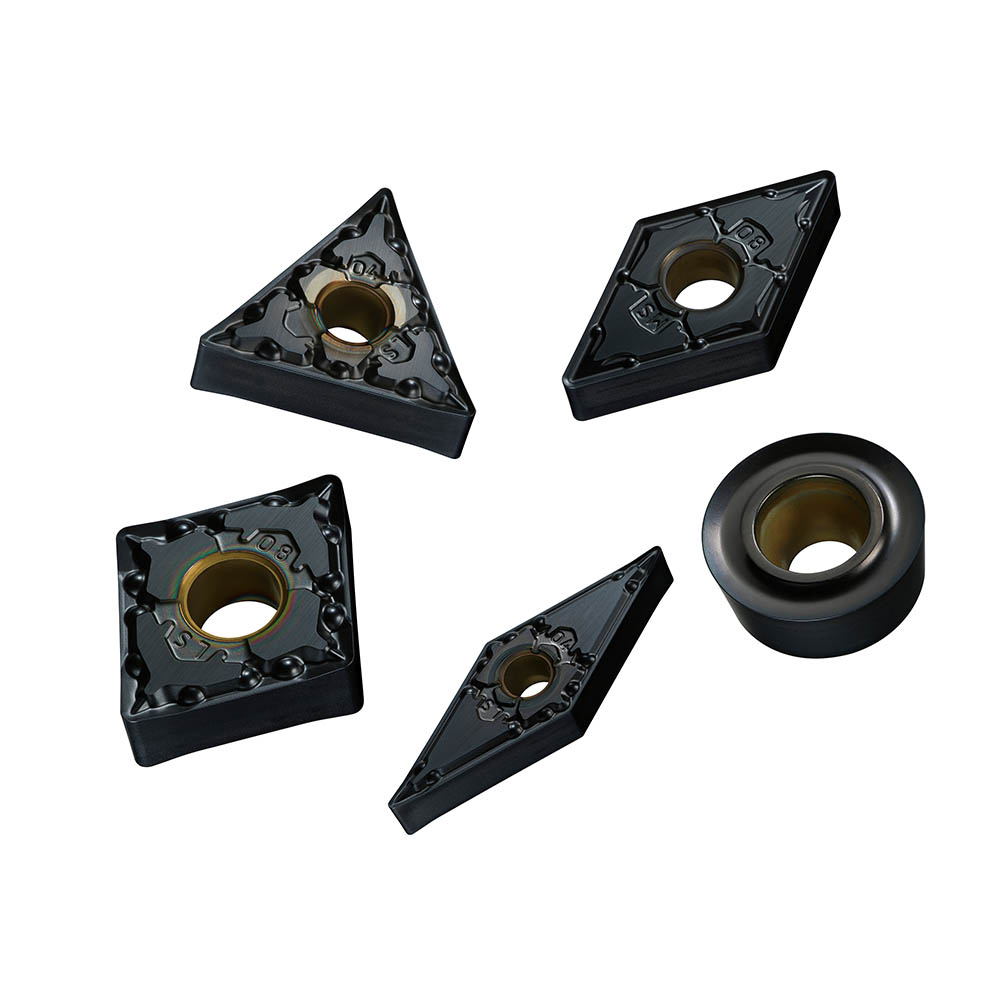
New grades
- Milling – MV1000: The MV1000 series includes 2 new grades, MV1020 and MV1030 for machining a wide range of materials from alloy and stainless steels through to cast iron.
For the WWX, WSX, WJX, WSF, VPX, AHX and ASX cutters - Turning – MV9005: This grade exceeds all current standards when machining heat resistant super alloys. A range of negative and positive inserts and 5 different chip breakers ensure the optimum combination.
Available in negative geometries CNMG, DNMG, SNMG, TNMG and VNMG types.
With a 7º RCMT and RCMX positive geometry types.
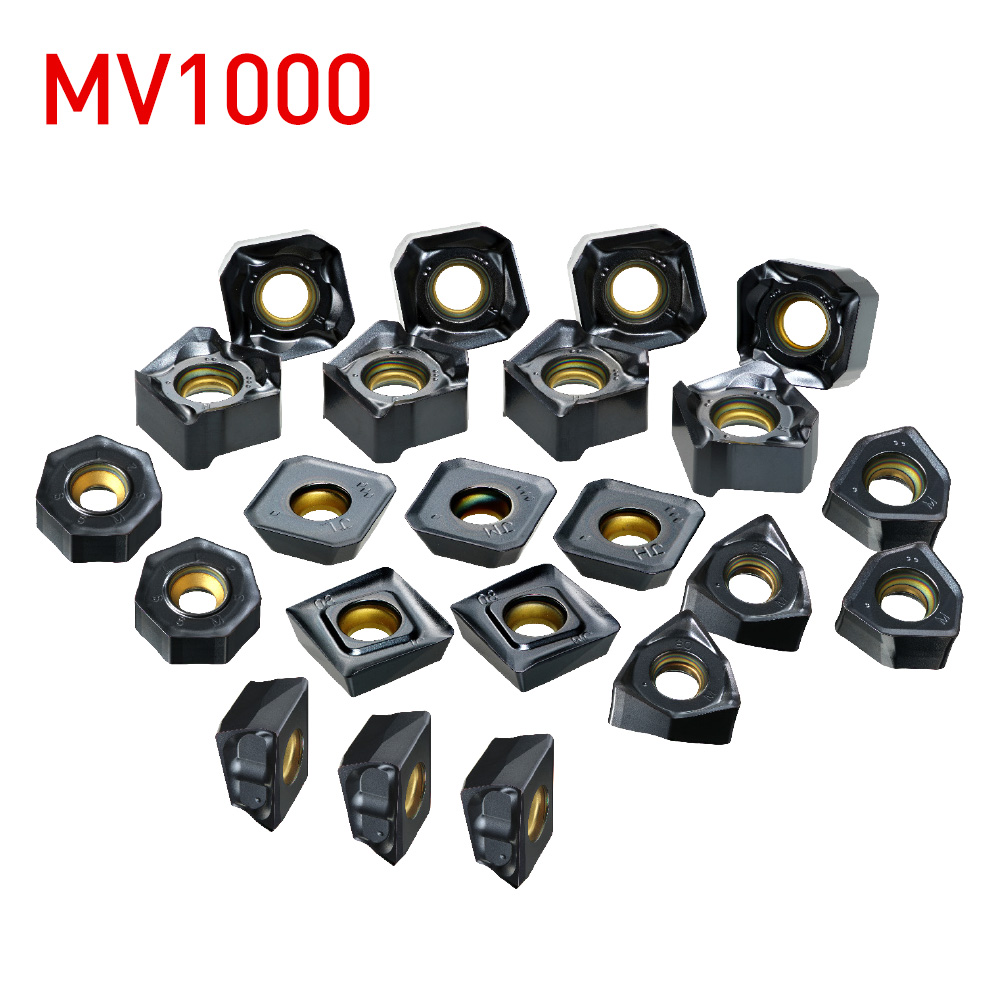
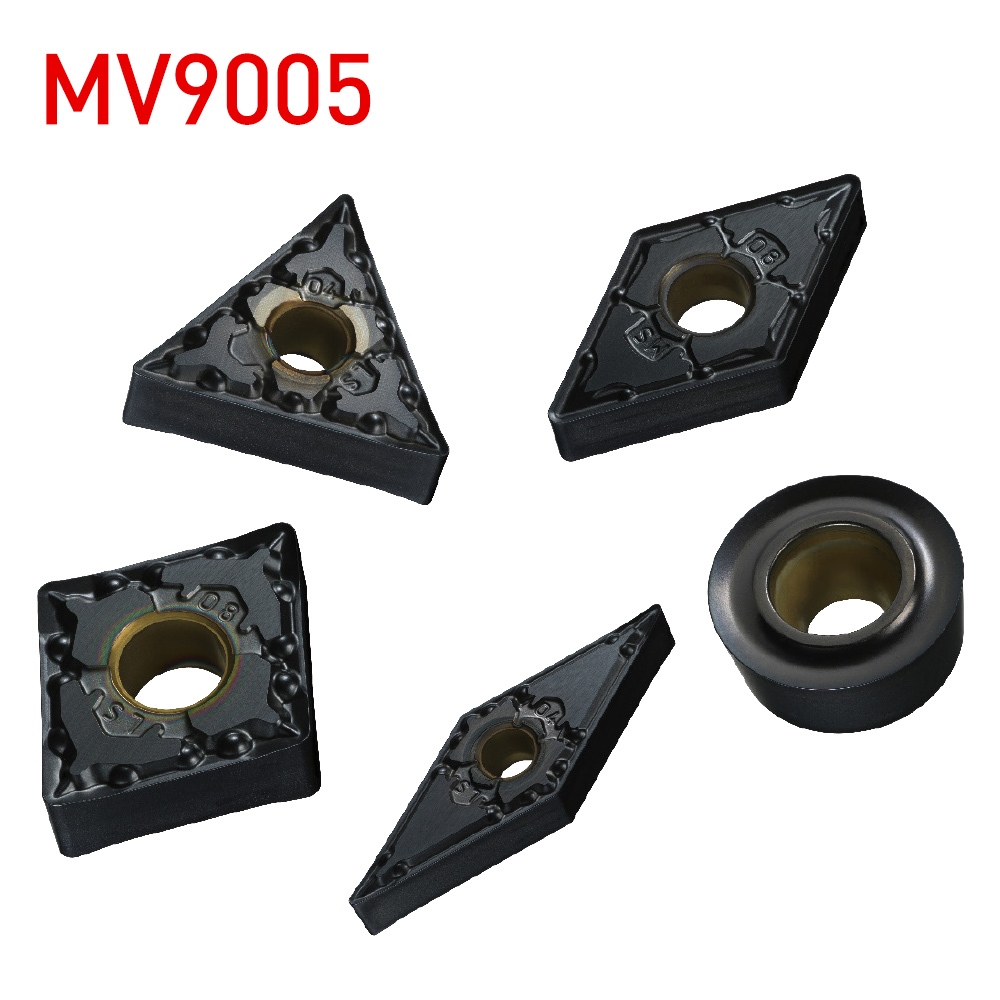

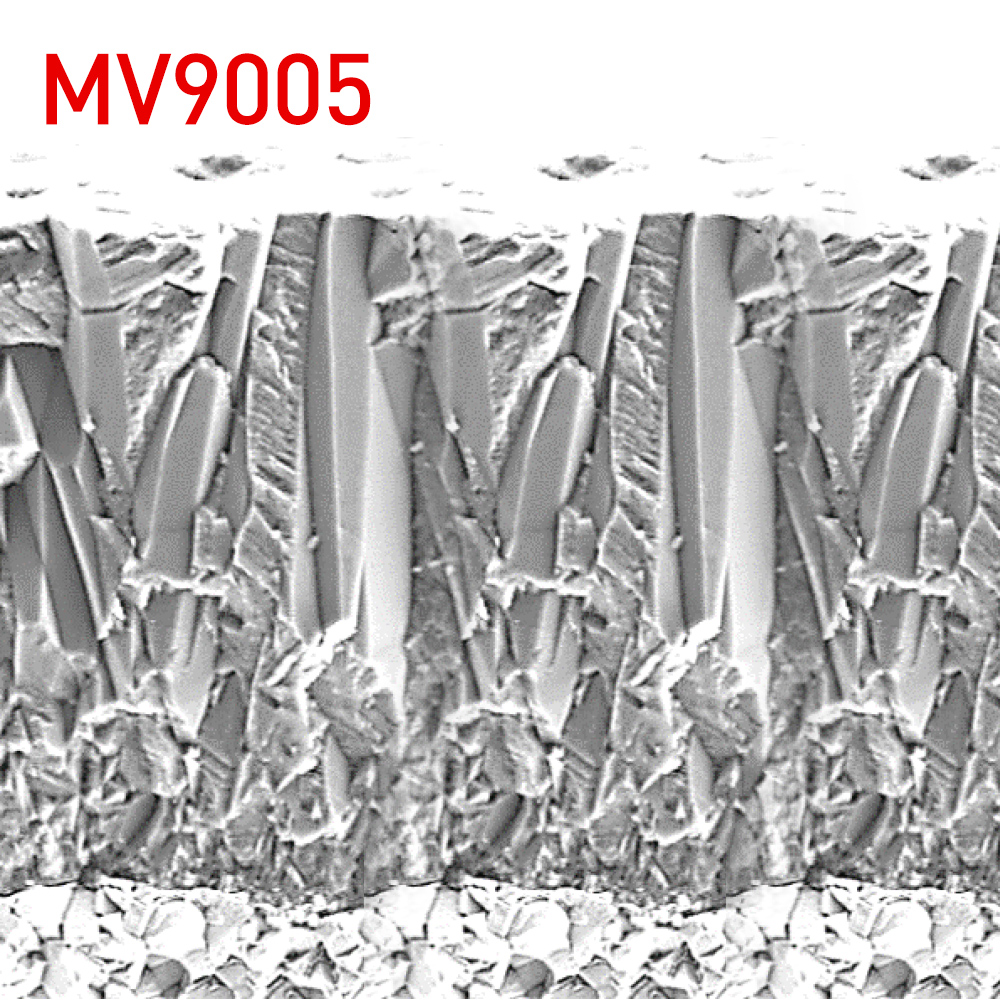