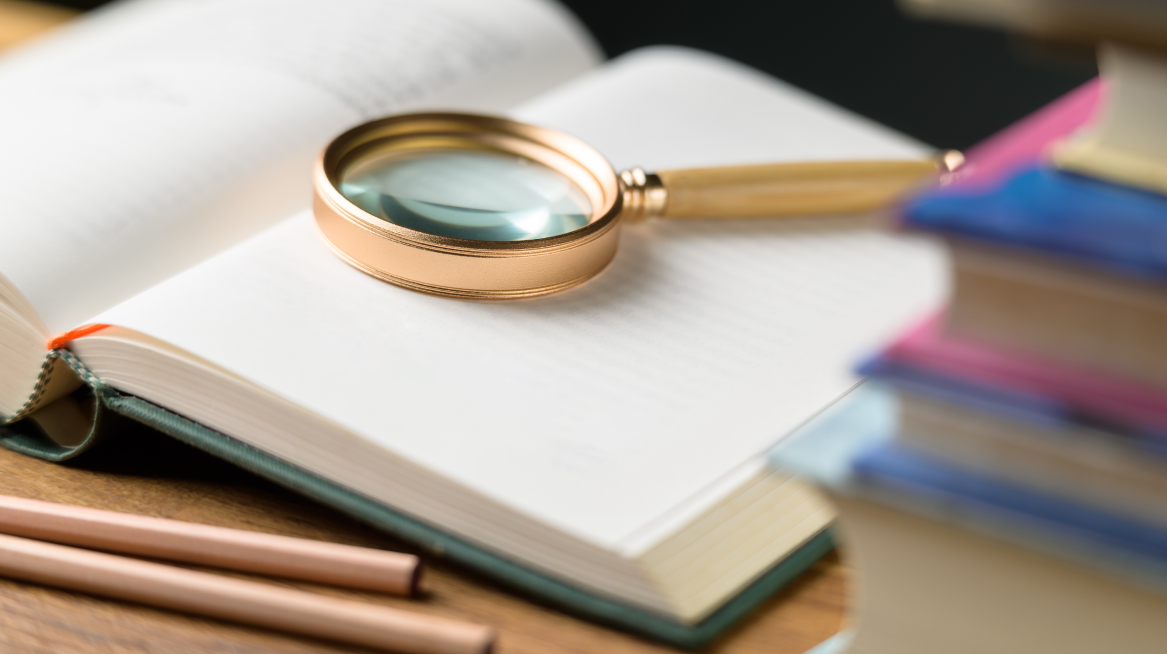
航空機以外も見据えて 加工品質と能率の双方を
材料別攻略法 CFRP
航空機の機体を中心に航空宇宙分野では、よく使われるようになった炭素繊維強化プラスチック(CFRP) 。最近では、軽量で強度の高い特性を生かして、さまざまな分野に活用が広がる。三菱マテリアルでは2017年から航空宇宙向けにCFRP加工用ドリル「MCシリーズ」を提供してきたが、将来を見据えてラインアップを広げている。岐阜製作所ドリル・超高圧工具開発部工具開発課の山本匡課長補佐は「従来から重要視する加工品質に加えて、今後は加工能率も求められる」と見通す。
自動車、医療、風力発電、スポーツ…
三菱マテリアルは昨年、CFRP加工用ドリル「MCシリーズ」のラインアップを7種類から10種類へと拡大した。そのうち「MCR」はCFRP単体の量産加工を意識して、生産性や加工品質の安定、工具寿命の長さに重点を置いて開発した。直刃でドリル溝も直線のタイプ。さらに、ワークからドリルが抜ける出口の周囲に切削抵抗(スラスト)がかからないように、先端には可変コーナーのR形状を採用した。ドリルの外径に近づくほど、放射線状に連続して減少する角度を付けた。
その結果、加工能率は従来品の約5倍となり、工具寿命は加工できる穴数が従来品の約1000穴から5000穴へと大幅に延びた。
山本課長補佐は「航空機以外にも、自動車の車体や医療分野、風力発電、スポーツレジャー用品などCFRPの用途が広がる。そういった分野では、従来よりも生産性や工具寿命が求められる」と分析する。
CFRP加工の難しさ
CFRPの加工中に起きるトラブルは、金属加工と全く異なる。CFRPは鉄に比べて、4分の1程度の軽さで約10倍の強度を持つ。また、耐腐食性や耐熱性、剛性の高さなどの特性もある。構造は炭素繊維の層と樹脂の層が交互に重なる。それぞれを見ると、炭素繊維は硬くてもろい。一方、樹脂は軟質で弾性変形しやすい。そのため、穴加工の際には1種類のワークで相反するような層を交互に貫く。
そんなCFRPの穴加工では、特に切断しきれなかった繊維によるトラブルが多い。穴の出入口では繊維が未切断で残る「アンカットファイバー」を生じる。また、穴の出口側には、スラストで「デラミネーション」が起きる。またCFRPと金属を重ね板にしたワークヘの加工もあり、金属部分の切りくずが穴から排出されるまでにCFRPの穴内部の壁面を傷付ける「バックカウンター」も頻発する。
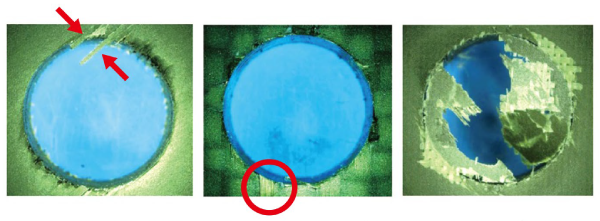
1本では不可能
同社では2000年代から航空機向けにCFRP加工用ドリルを提供してきた。航空機用部品に使うCFRPの樹脂には、熱硬化性と熱可塑性が混在する。CFRPにアルミニウム合金やチタン合金の補強材を重ねた「スタック材」もある。
加工方法は3種類で、マシニングセンタなどを使う機械加工と、組み立て現場で専用の動力工具をジグに押し当てて機械送りで加工するケース、同じく組み立て現場で人がハンドドリルを持って手動送りで加工する場合に分けられる。
このように異なる材料や加工方法がある中でも、当初は1種類のドリルで全ての状況に対応できる工具開発を目指した。しかし、万能工具を目指すと、使用場面によっては、顧客の要求に足らないドリルになりかねなかった。そこで、使用環境に合わせた特徴を持つ専用ドリルをMCシリーズと名付けて17年に7種類発売した。
その中で「MCA」はCFRPとアルミ合金のスタック材の専用ドリル。ドリルがCFRP層を貫通してアルミ層を削っていく際に、アルミの切りくずがCFRPの穴壁面の一部を削り、CFRP層とアルミ層の穴径に差が生じる。このバックカウンターを防止するために、溝形状の設計をーから見直した。
特にドリルの溝幅に工夫を加えた。一般的なドリルの溝幅は全て一定だが、MCAは先端部分から根本に向かうにつれて徐々に溝幅を広げた。最初は細い溝で小さくまとまった切りくずを生成し、その後は大きな溝の中を穴壁面に干渉することなく流れていく。この溝設計には、深穴加工用ドリルの技術を応用した。
「穴壁面の品位を高めるため、切りくずの排出方法はスタック材加工と深穴加工の共通課題だった。社内のノウハウを上手に応用できた」と山本課長補佐は振り返る。
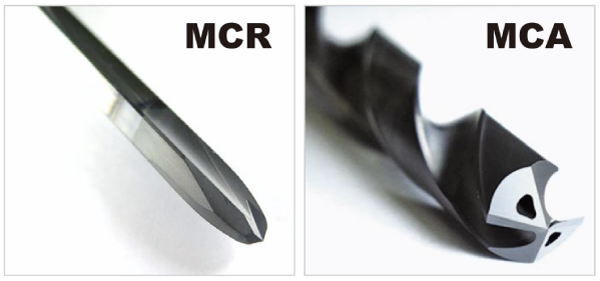
産ロボの活用も視野に
加工状況は日々、変化する。例えば、組み立て現場でよく使われる動カエ具。従来は圧縮空気で稼働していたが、電動式に置き換わっている。電動式になると、被削材ごとに切削条件を設定したり、ステップ加工をするなど、臨機応変に対応できる。そうするとCFRPと金属が重なるスタック材を加工する際には有利になる。また、主軸モーターの電流値の解析もでき、工具の損傷や摩耗と関連付けて分析すれば、交換時期の見極めも可能になる。
さらに自動化も進む。航空機の組み立て現場で作業者が動力工具を使っていた工程を、産業用ロボットに置き換えるための研究が進む。手加工がロボットに置き変われば、加工条件も変わり、必要な工具形状も変化する可能性もある。
山本課長補佐は「加工条件だけでなく、素材の進化も著しい。CFRPの用途も広がる。われわれも柔軟に変化して対応していきたい」と意気込む。
(西塚将喜)
ニュースダイジェスト社 生産財マーケティング12月号掲載記事
PDFファイルはこちら
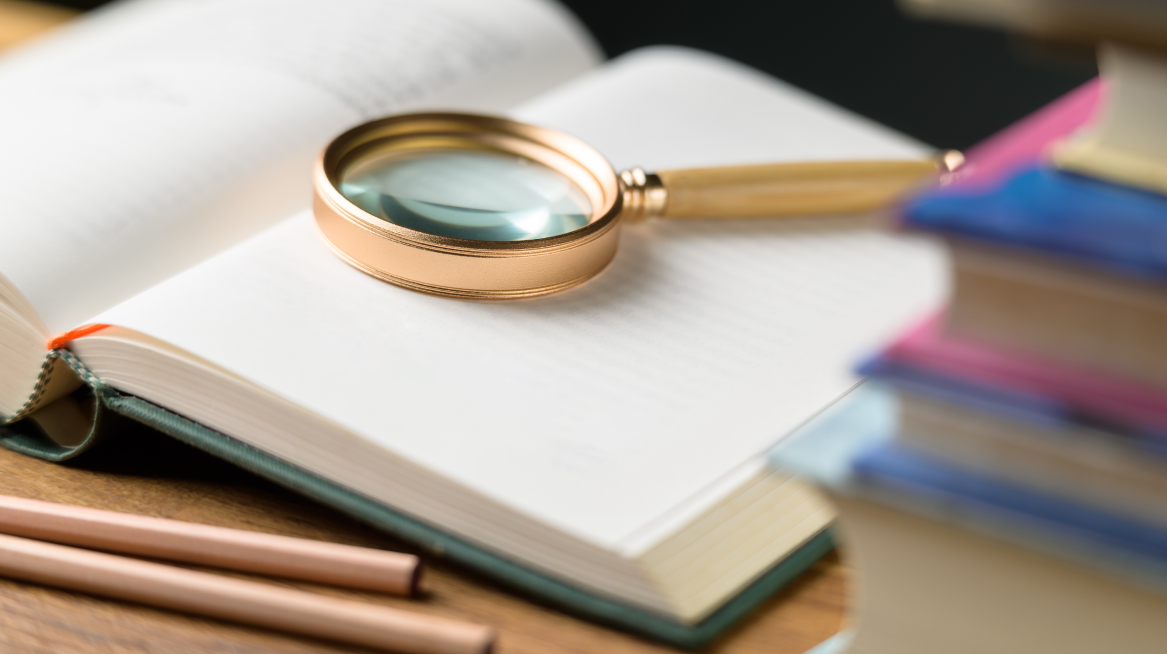