VPX Series
Multi-functional tangential insert cutter for high efficiency machining
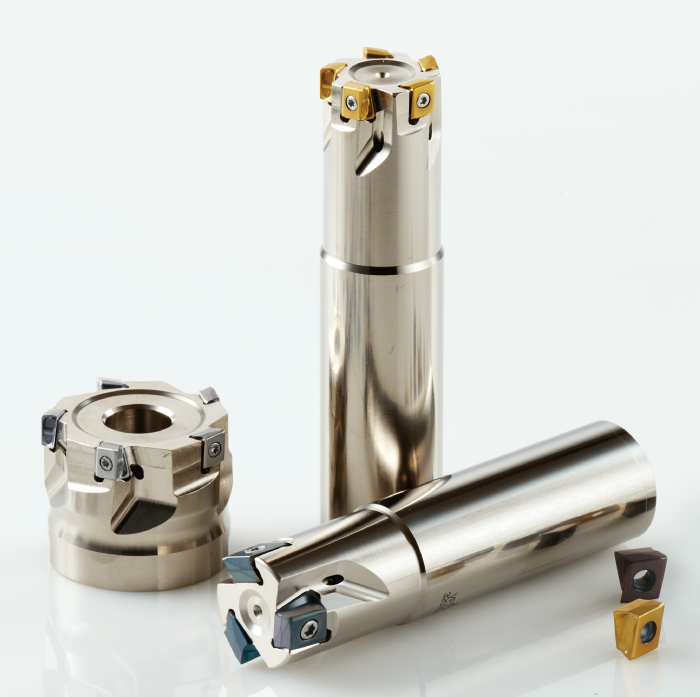
Boost Your Milling with a Tough Tangential Insert !
TOUGH & MULTI
Extremely rigid and functional.
Our thoroughly calculated design will completely change how you see the tangential cutter.
About TOUGH
Pursuing the tough machining characteristic of tangential blade inserts.
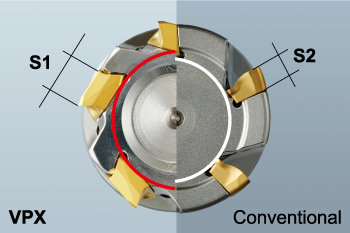
By arranging the inserts tangentially, high holder rigidity is secured. Also, because the part subjected to the highest loads during machining is larger (S1>S2), it has great fracture resistance and can be used without worry for high efficiency machining.
The wide seating surfaces provided allow the insert to clamp on more firmly. Suppresses deviation of the insert caused by vibrations during machining.
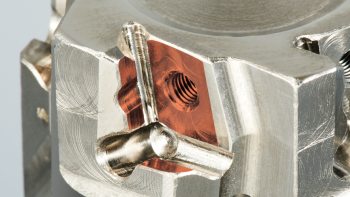
Comments from developersDurability born through repeated destructive tests.In order to improve durability, we began development by first applying a load to the cutter until it broke. After analyzing the reasons it broke, we produced an improved version then broke that as well. We repeated this process until we were satisfied with the results. As a result of this pursuit of durability through thorough destructive tests, we were able to come up with a cutter that is ideal for unmanned operation and high efficiency machining. |
About MULTI
Solving problems as a multi-functional cutter.
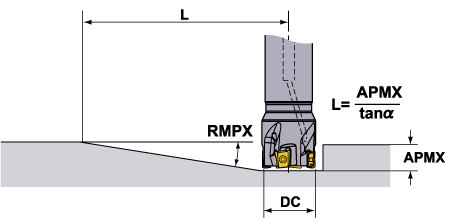
Comments from developersThrough trial and error, we’ve solved industry problems.The surface-to-surface balance of the insert is what allows the multi-functionality of ramping to be achieved, while maintaining the good chip ejection and the cutting performance inherent to tangential blade cutters. Most tangential blade cutters must be changed out with dedicated inserts for ramping. We made it a priority to unify these two styles of inserts, so as to avoid the trouble of managing two sets of inserts, and prevent installation mistakes.By focusing on the surface design of these new inserts, and through repeated trial and error, we were able to resolve one of the major issues in the industry. |
Different types of milling cover a wide variety of situations.
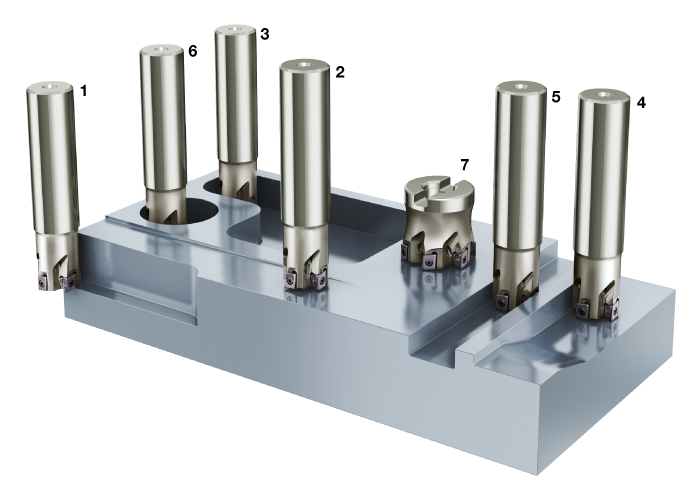
1. Shoulder Milling 2. Ramping 3. Pocket Milling 4.3-D Profile Milling
5. Slot Milling 6. Helical Milling 7. Face Milling
Inserts
Double-sided insert that has revolutionized tangential blade machining.
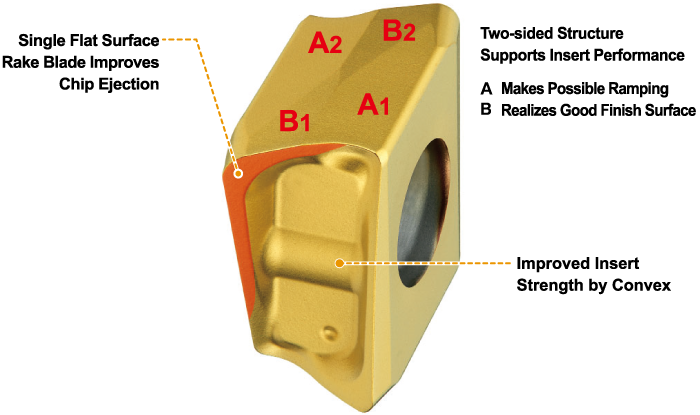
Comments from developersAn insert shape that was possible to design, but difficult to commercialize.The shape of the insert makes it tough while still enabling multi-cutting. It has been extremely difficult to move from the prototype, to maintaining a stable shape as a product. It is not an exaggeration to call this product, which has finally been commercialized through repeated improvements, the jewel of Mitsubishi Materials technology. |
High Wall Surface Accuracy
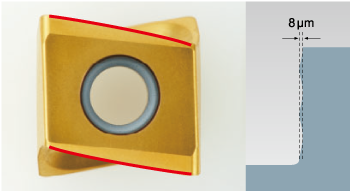
Large R-blades Achieve a Good Finish Surface
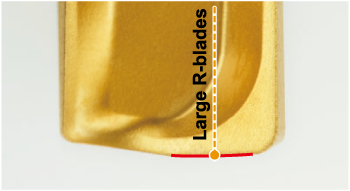
Insert Grades for a Wide Range of Materials
MP6100/MP7100/MP9100 Series
TOUGH-Σ Technology
A fusion of the separate coating technologies; PVD and multi-layering provides extra toughness.
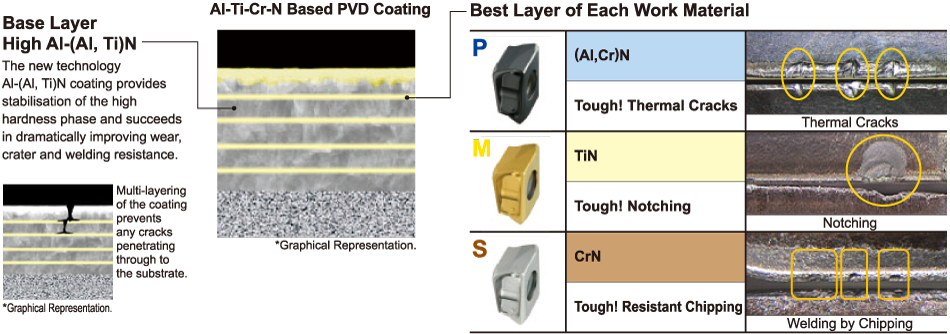
CVD Coating MC5020
First recommendation for cast iron milling.
MC5020 has excellent wear resistance and also controls thermal cracking and chipping that are common when machining ductile cast iron.
Black Super-smooth Coating
Black super-smooth coating prevents abnormal damage such as weld chipping.
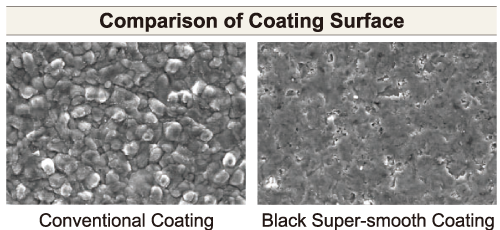
Chip Breaker System
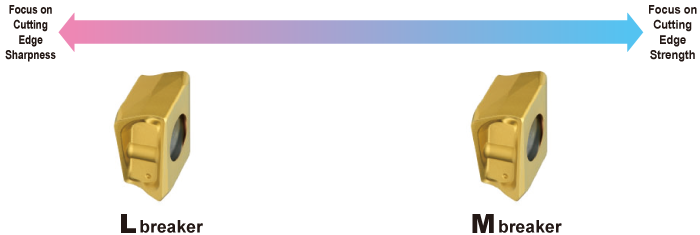
Application Examples
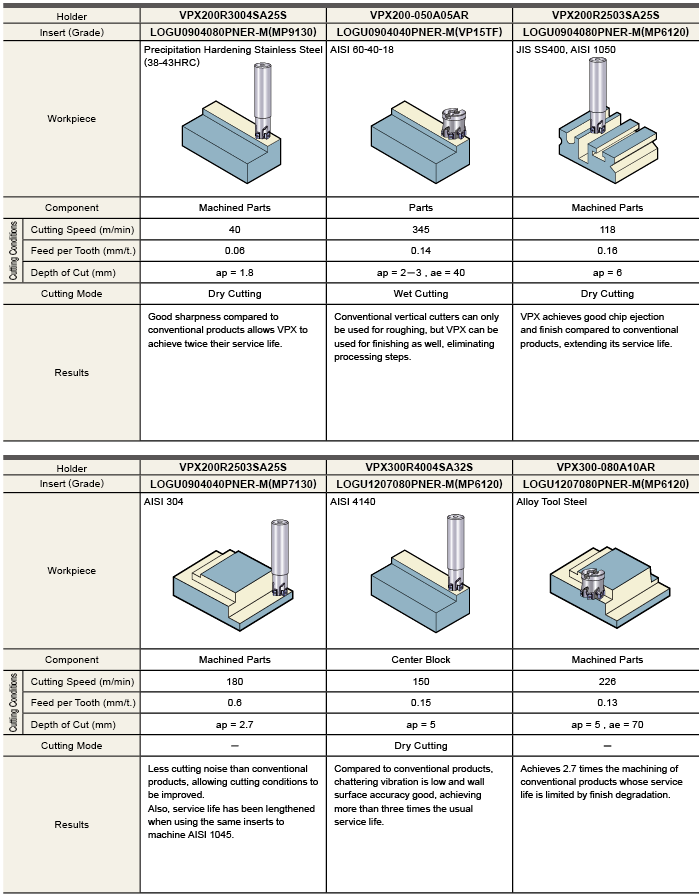
The examples shown are actual applications and can differ from the recommended cutting conditions.
Technical consultation from here
24/7Contact form